AQL Standard: 5 Main Categories of Product Defects
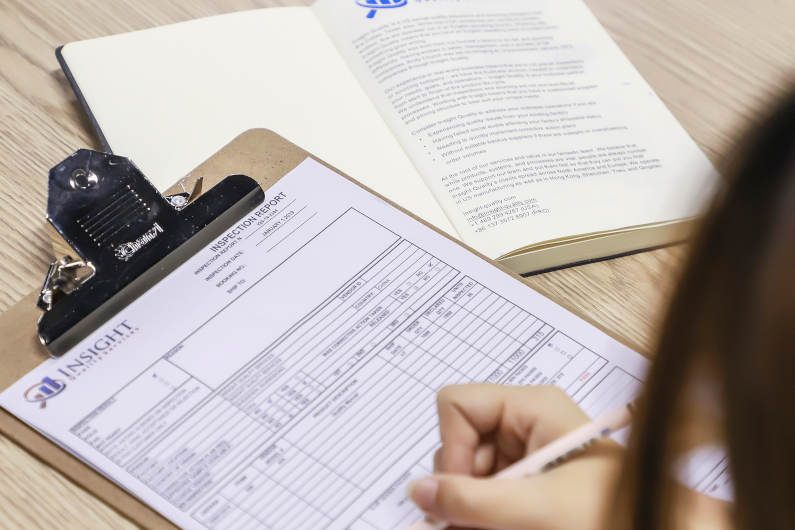
How can you be sure that your organization’s products are free of defects? The answer to this question isn’t as obvious as it may seem at first, which makes it all the more important to know exactly what constitutes a product defect and how you can achieve defect-free production in your manufacturing processes. In order to do so, it’s essential to understand the ISO 13485 standard and the SA8000 standard, both of which provide information on how to identify and prevent defects within your product design and production cycle, respectively.
What is AQL?
AQL, or average received quality, is a measure of how often products that are received by a manufacturing plant are defective. It is determined by dividing the number of defects by the number of products that were received.
Product defects can take many different forms, but they all have one common goal: They are mistakes made during the manufacturing process that result in the creation of defective products.
There are many different categories of product defects, and each one has its own set of consequences. Some of the most common categories include design defects, manufacturing defects, and assembly defects.
Each category has its own set of criteria that must be met in order for a product to be considered defective. Design defects occur when the design of a product is flawed and can cause it to fail in performance or usability. Manufacturing defects happen when components or materials in a product are not correctly manufactured and can lead to it being unusable or dangerous. Assembly defects occur when parts or assemblies in a product are not put together correctly and can cause it to malfunction or break.
By understanding what constitutes a defect and how it affects your products, you can ensure that they’re delivered to your factory in good condition and free from any potential problems.
Defects and AQL
Product defects can be classified into five main categories: physical properties, performance, appearance, function, and packaging. For each category, there are different inspection levels that must be met in order for the product to be considered compliant.
For example, the SA8000 audit looks for compliance in social and environmental standards, while the ISO 13485 audit assesses medical device quality management systems.
There are different types of product defects, and each has its own consequences. Some common types of defects include:
-Incorrect material specifications: This can lead to products that are not as strong or durable as they should be.
-Injuries caused by the product: This includes everything from skin rashes to serious injuries that can result in death.
-Non-conformities with customer orders: This often happens when the manufacturing plant is not able to meet customer demand for products.
All of these types of defects can have a negative impact on a company’s reputation and ability to sell products. To avoid these problems, it is important to have a robust quality control program in place. This will help to ensure that products meet customer expectations and are free of defects.
Five Main Categories of Product Defects and Standards
There are five main categories of product defects and standards that manufacturers must adhere to.
These categories are design flaws, manufacturing defects, materials defects, performance defects, and marketing defects.
- Design flaws include anything that goes wrong with the look or function of a product. This could include things like poor ergonomics or incorrect design specifications.
- Manufacturing defects occur when products are made improperly. This might involve using the wrong materials or using poor techniques during the manufacturing process.
- Materials defects can occur when the components of a product don’t meet the required standards. This could lead to devices not working as intended or parts that break easily.
- Performance defects refer to how a product performs in comparison to its specifications. This could involve a product failing to meet its basic functions, such as heating up quickly or lasting long on a battery charge.
- Marketing defects refer to any errors or omissions in the way a product is marketed. This could involve untrue claims about the product or misleading advertising.
Key Points to Remember
There are many types of product defects, and each can have a different impact on a company’s bottom line.
Product defects can take many different forms, but some of the most common categories are design flaws, manufacturing defects, and errors in labeling or advertising.
Design flaws occur when the design of the product is not correct, which can lead to problems such as crashes or fires. Manufacturing defects occur when the products are made incorrectly, which can lead to safety hazards or performance issues. Errors in labeling or advertising can result in customers buying products that they do not actually need or want.
Each type of defect has its own unique consequences for a company. It is important to understand the key points to remember when it comes to product defects, so that you can make informed decisions about how to protect your business!
Conclusion
When it comes to product defects and Quality Control Inspection, there are a few main categories that can affect your product. Some of the more common categories include manufacturing defects, design defects, and sourcing defects. In each case, you should be aware of what to do if you experience a defect in your product and how to prevent it from happening in the first place. By following these tips, you can ensure that your products are delivered without any problems or complaints from consumers.